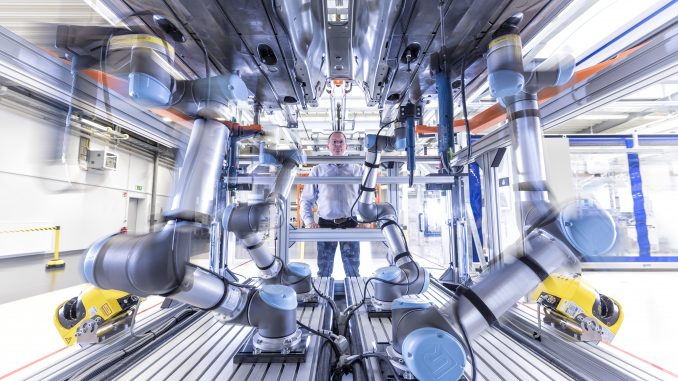
Az Audi Tech Day nem amatőröknek való. Úgy záporoztak az ipar 4.0, digitalizáció, együttműködő robot, startup, 3D nyomtatás, modularitás, taktidő, smart factory, lézer, hozzáadott valóság, okos szemüveg, big data, data lake, CKD, munkatárs irányítás kifejezések, mint egy Calgary Flames Vancouver Canuks hokimeccsen a pofonok. Ingolstadtban jártunk, okos gyártást láttunk.
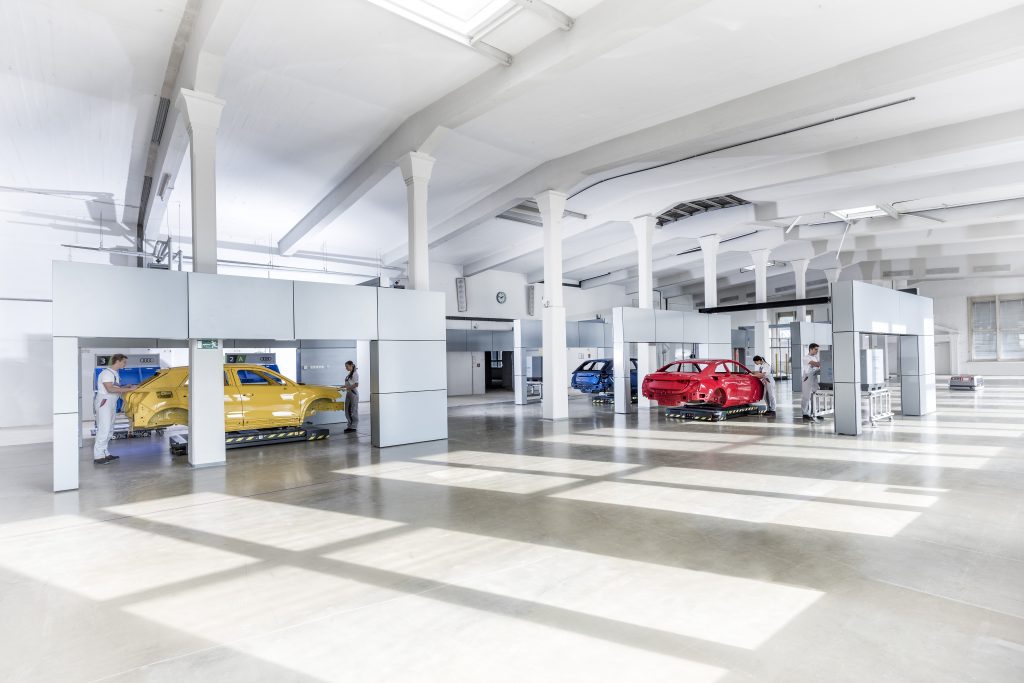
Büszkék lehetnek a győriek a gyárukra, mert az Ingostadtban megszervezett technológiai bemutatón sokszor szóba került Győr. Számos világújdonság úttörője vagy első alkalmazója az Audi Hungaria, nem hiába érkezik majd hozzánk a villanymotorgyártás és még a villanyautó-összeszerelés sem került le a napirendről.
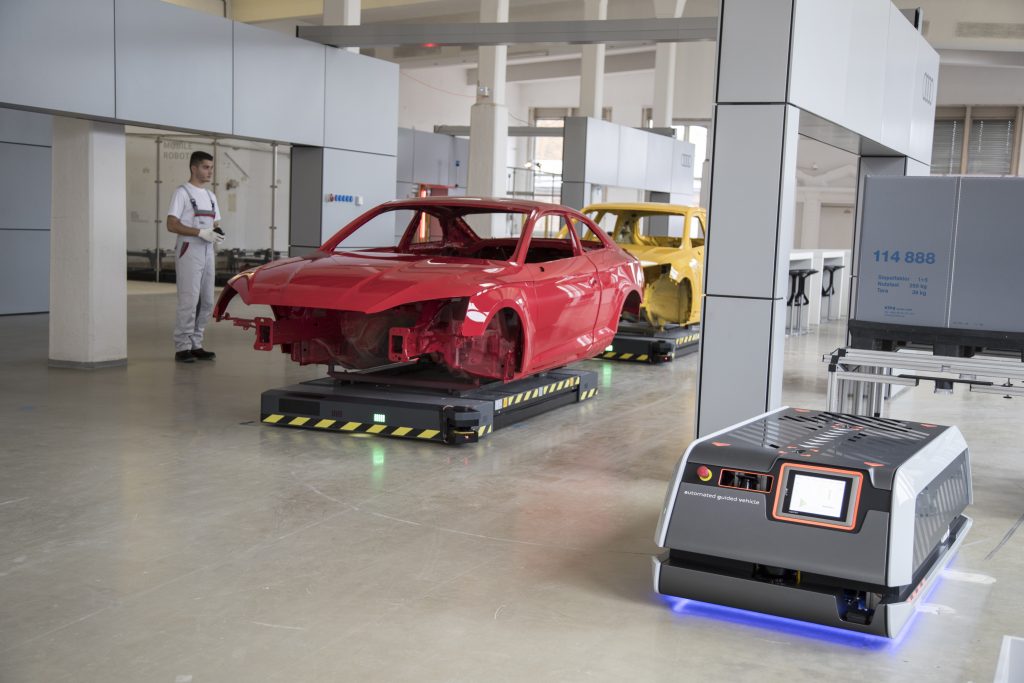
Az Audi az okos gyártásban érdekelt, és mint a smart factory előfutára, az autó- és motorgyártását ebben a szellemben alakítja át. A jövő gyárában az adatok köré rendeződik minden, hiszen az adat a jövő szene, a jövő mozgatója. Aki az adatot megérti, kezeli és hasznosítja, az lesz a jövő nyertese. Az Audinál a gyártósorok jövőjét moduláris szigetekként képzelik el, ahol a járművek önműködő, automatizált eszközök segítségével nem egy zárt soron lineárisan, hanem a következő fázis ismeretében egyedileg, a megfelelő időben érkeznek meg a megfelelő szerelési állomásra. Ezt nevezik moduláris összeszerelésnek és Ingolstadtban egy korábbi textilgyár csarnokaiban ebből kaptunk ízelítőt.
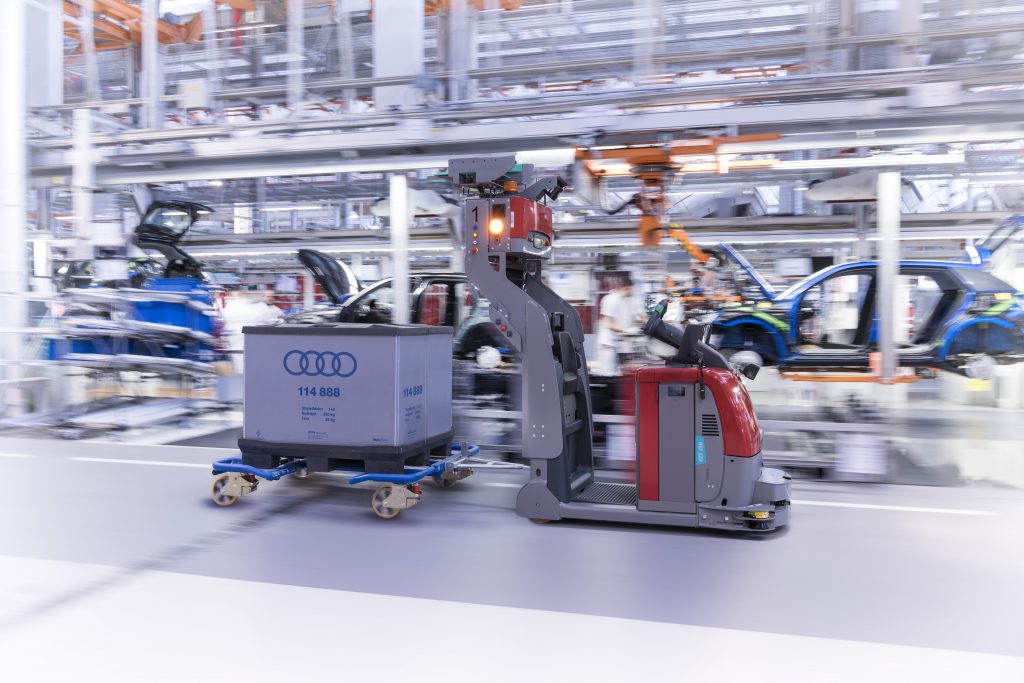
Moduláris összeszerelés
Egy startup cég műhelyében járunk, ahol nem az autógyárakban megszokott rendezettség uralkodik, a falakból vezetékek lógnak, OSB-lappal tömködték be a lyukakat, ruha-, vagy húsakasztó kampók lógnak mindenfelé, szabadon látszanak az épületgépészeti részletek, hibás és hiányos a festés, illetve a burkolat. Mintha szándékosan lenne ilyen. Itt működik az arculus, egy Audinak dolgozó startup. Vezetője, Fabian Rusitschka korábban az Audinak dolgozott közvetlenül, most a moduláris összeszerelés prototípusát álmodja életre. A kulcsszó a testre szabás. Olyan széles igényeket kell kielégíteni, hogy a lineáris gyártósor a jövőben nem képes hatékonyan megfelelni a szinte már egyedinek (más-más piaci és jogi környezet, számtalan variáció, innovatív technológiák) számító, de ugyanakkor nagy darabszámú termelés kihívásainak. A moduláris szigetek időt és pénzt spórolnak, miközben nem járnak leépítéssel, sőt a dolgozóknak akár hosszabb időt is adnak a kézi összeszerelésre. Az alkatrészek, járművek vezető nélküli eszközökön közlekednek, a rádióvezérlésű rendszerben a járművek lézeres szenzorjaik segítségével mozognak, a gyártásban nem következhet be fennakadás, vagy torlódás.
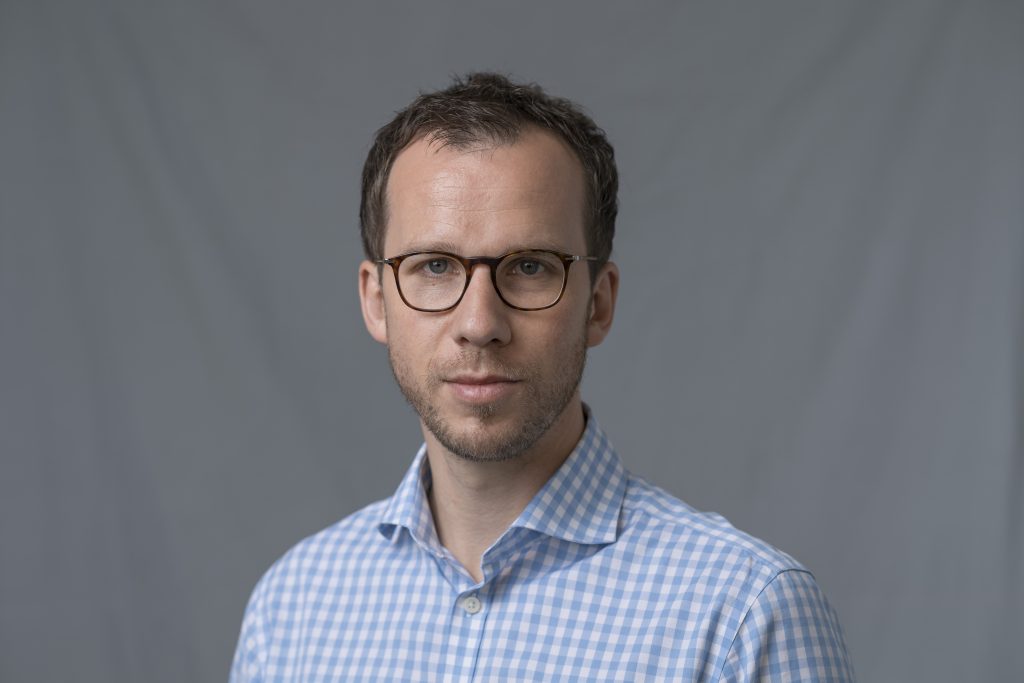
Hubert Waltl, az Audi AG gyártásért és logisztikáért felelős elnökségi tagja szerint a vállalat 20 százalékkal javíthatja a modularitás bevezetésével a termelékenységét. Örömteli, hogy az önszabályzó rendszert először Győrben tesztelik élesben (elektromos motorok gyártása), majd két további alkalmazását (Ingolstadtban és a Lamborghini Santa Agata-i gyárában) is megkezdik a közeljövőben. A termelés és a logisztika nem különül el egymástól, hanem még jobban integrálódik, szervessé válik.
Önvezérlő járművek
Az Audi technológiai napján közelebbről is megismerkedhettünk Paulával, azzal a saját fejlesztésű vezető nélküli járművel (agv), amely már jelenlegi is dolgozik az ingolstadti szereldében, Audi A3-asok és Q2-esek klímarendszerét szállítja a sor megfelelő állomására.
A technológiai központban az önjáró prototípusai mellett új fejlesztéseket is bemutattak a szakemberek. Az okos Claus elnevezésű munkatárs-támogató rendszer kamerák segítségével monitoron megjelenített fázisfotókkal és teendőkkel segíti például egy igen bonyolult ajtómodul pontos, hibátlan és gyors összeszerelését. Egy másik alkalmazás az fej feletti munka megkönnyítésére irányul: kézi, vagy automatizált csavarozók helyett kis robotkarokkal végezteti el például a padlótakaró műanyag lemezek rögzítését úgy, hogy egymás után különféle autótípusokkal szerszám, csavar és technológia csere nélkül dolgozik, az ember csak felügyeli a gép munkáját (ember-robot együttműködés).
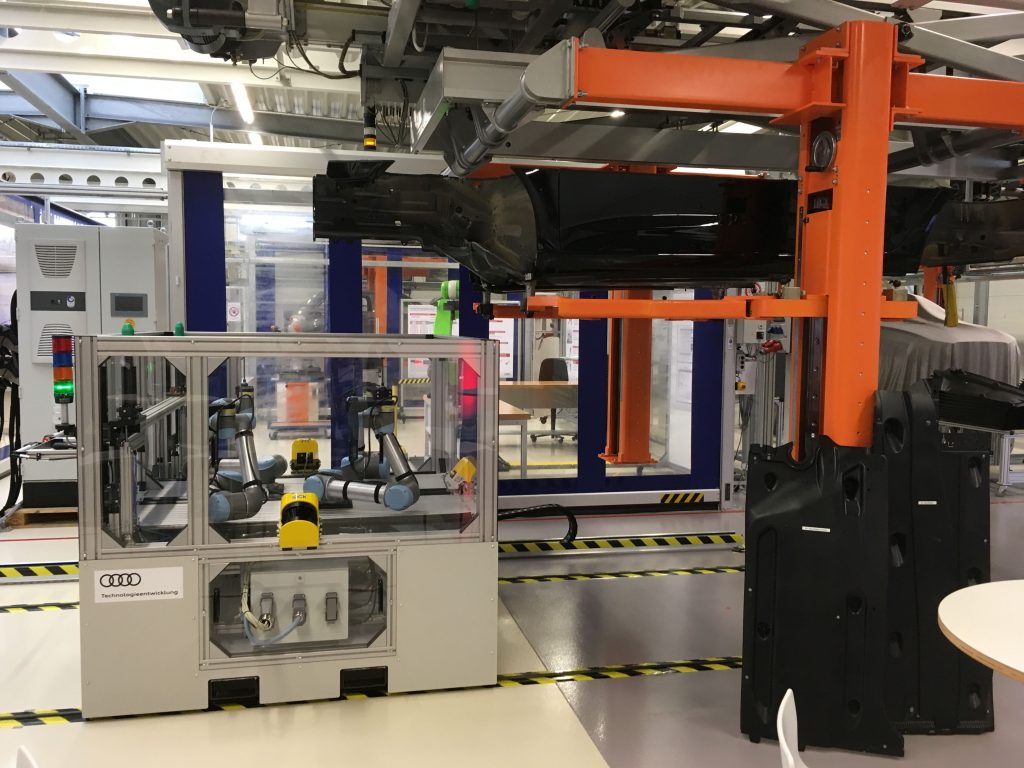
A technológiai labor leglátványosabb és legnagyobb érdeklődésre számot tartó alkalmazása az állatvilágból lopta az ötletet. Olyan fogófejjel ellátott roboton dolgoznak az Audinál, amely szinte mindenféle felületű, formájú és alakú alkatrészt képes megragadni és például a moduláris összeszerelést kiszolgáló alkatrészellátó dobozába előkészíteni. A Festo közreműködésével olyan gumiszerű fogót tettek a robotkarra, amely akár a kaméleon nyelve, rátapad mindenre. A pneumatikus rendszer könnyedén felemel egy navigációs antennát, négy szellőző rostélyt tartalmazó tartót, egy kábelkorbácsot vagy 5-6 apró csavart. Ezeket természetesen a megfelelő fakkokba teszi. A robot még tesztelési fázisban van és egy kicsit még lámpalázas: az újságírók előtt a fejlesztői legnagyobb megrökönyödésére elejtett egy csatlakozókábelt.
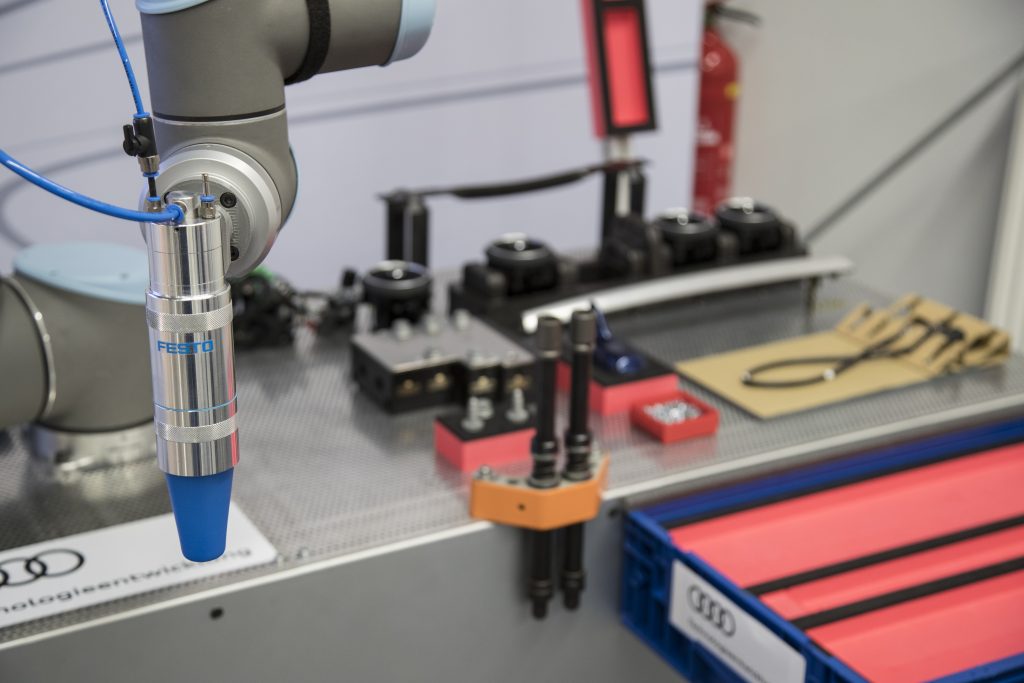
Okos eszközök
Egy másik ingolstadti helyszínen a gyártási laborban a távszerelés rejtelmeibe vezettek be, éppen egy győri kolléga által jelzett álproblémának jártak utána Ingolstadban egy kamerával rendelkező tablet, illetve okos szemüveg segítségével. A segítőközpont távolról elér minden adatot, a kamera révén lát is, az utasításokkal a helyszínen elhárítható a probléma.
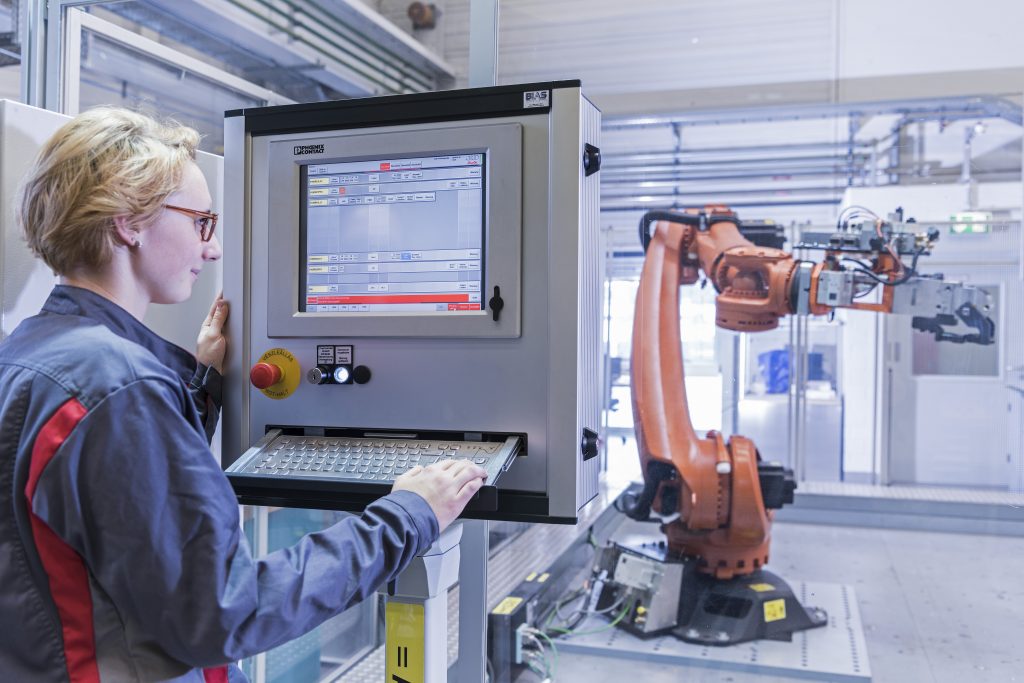
A 3D nyomtatás már nem a jövő, hiszen Győrben is készülnek alkatrészek a kísérleti motorfejlesztő számára, de az ingostadti nyomtatók különböző generációinak az alkalmazása azt jelzi, hogy fémből (acél, alumínium, titán) egyre gyorsabban készülnek el a bármilyen bonyolultságú alkatrészek. Ingolstadtban már 400 milliméteres alkatrészt is tudnak nyomtatni, egy kiló fémet két nap alatt. A sorozatgyártás természetesen még nem téma, óriási költség a nyomtatás, de egy-egy különleges Audi R8 modell ma is kaphat nyomtatott alkatrészt. A présüzem használja azt az audisok által kifejlesztett optoelektronikai mérőrendszert is, amely a lemez olajbevonatával ellenőrzi, hogy van-e bármilyen karcolás, hajszálrepedés vagy kosz a présszerszámon, vagy a lemezen.
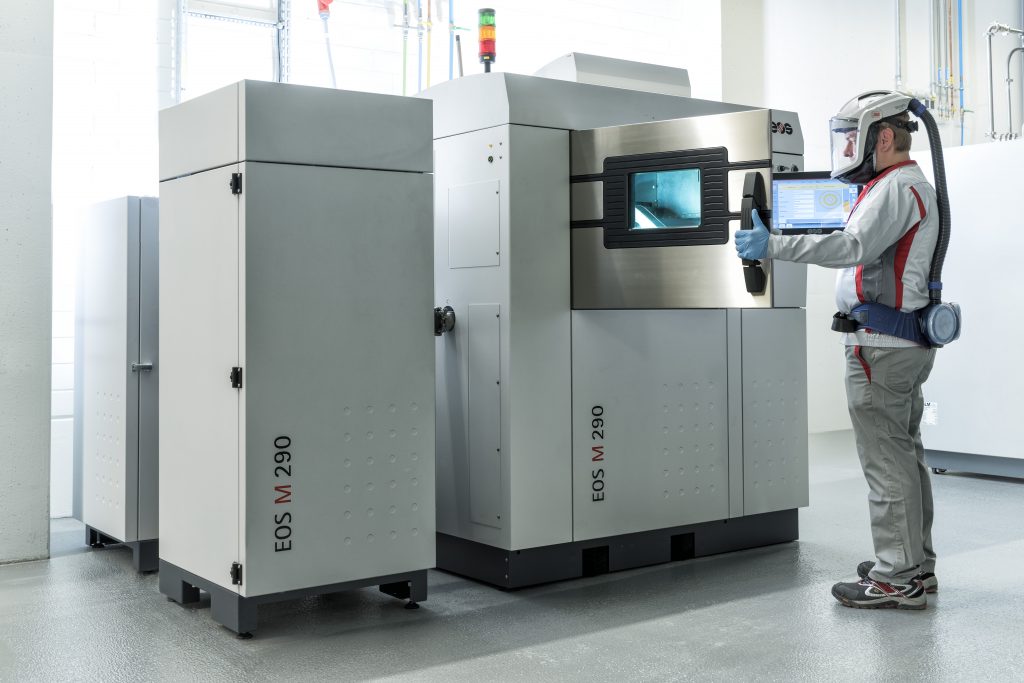
A produkciós labor legunalmasabb szegletében matematikusok adatelemzésekkel próbálták fenntartani az érdeklődésünket. Annak ellenére, hogy a jövő gyára és gyártása ezeken az okos analíziseken és az ezekből fakadó következtetéseken, sőt előrejelzéseken, üzleti intelligenciákon alapulnak, a figyelmünket jobban lekötötte egy másik helyszínen, másik csoporttal zajló játék. Ebben a produkciós labor tudósai a virtuális világot építik be a termelésbe. Hátunkon viselt számítógéppel és zombiölős PC-játékokban alkalmazott VR-szemüvegekkel nézhettünk bele egy-egy alkatrész – Audi TT műszerfal – rejtelmeibe. Bár kívülről nevetséges volt a szellemekkel folytatott cicaharc, a virtuális világban komoly feladatot oldottunk meg koboldszerű társaimmal: elhárítottuk az akadályát annak, hogy a fejegység bekerüljön a helyére. Az alkalmazás segítségével megvalósítható a térugrás, egymással több összekapcsolt szakember különböző helyszínekről tarthat úgy megbeszélést, hogy közben egy virtuális térben, virtuális eszközökkel valós feladatokat oldanak meg. A kiterjesztett és virtuális valóság egy elemibb alkalmazásában Google-szemüveg alkalmazásával tudjuk egyszerűsíteni a szerelést: QR-kód leolvasásával a szemünk előtti apró monitoron jelennek meg az aktuális utasítások, vagy éppen tanvideók, a mozdulatsorok megerősítéséhez elég egyszerűen megérinteni a szemüveg szárát, máris jön a következő feladat.
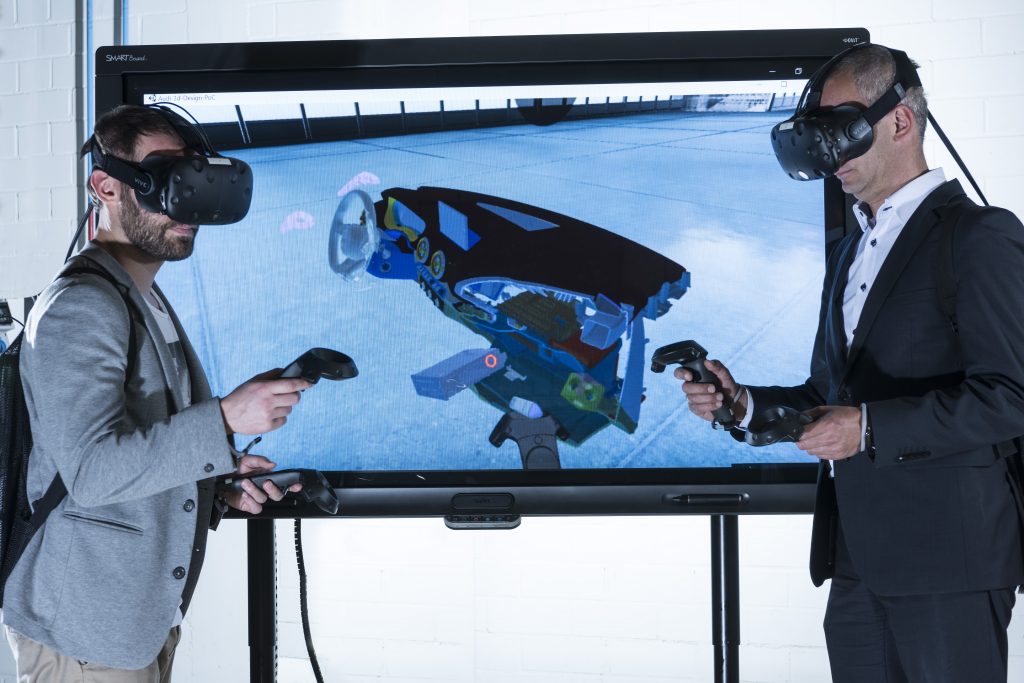
A technikai napon az Audi csak egy töredékét mutatta meg mindannak az innovációs tudásnak, amellyel rendelkezik és amellyel a jövő Győrben is épül. Kimaradt például a programban beharangozott drónos alkatrészröptetés. Minden bizonnyal ezt legközelebb az Audi Hungaria győri gyárában majd bepótoljuk.
Biró Csongor