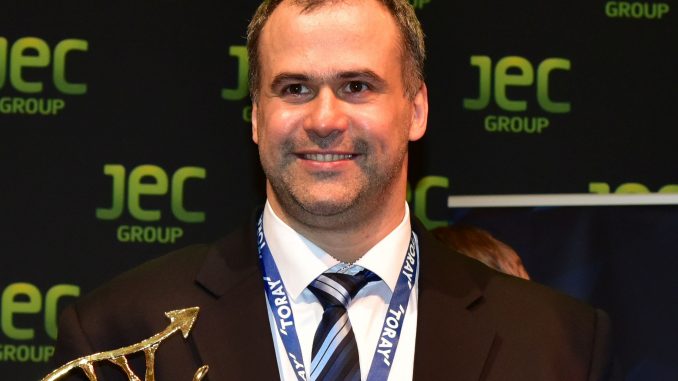
Az Evopro-csoport busz üzletágának igazgatóját kérdeztük a kompozit buszgyártás technológiájáról és tapasztalatairól.
– Milyen mennyiségtől válik nyereségessé a kompozit gyártás?
– A kompozit testek gyártásán most is elérhető kisebb nyereség, de legfontosabb az, hogy mikor érjük utol a hagyományos fém busztestek árszintjét. Ez, a költséghatékonyság 2-300 darab gyártásától megvalósul, de az egyes moduloknál eltérően számít a gyártott mennyiség. A fém ötvözők erőteljes drágulása miatt a korrózióálló acélok ára is drasztikusan növekszik, így ez a különbség egyébként olvadóban van. A moduláris felépítésű kompozit test és az alkalmazott funkcióintegrálás előnye, hogy jobbára sztenderdizált elemekből épül fel a busz. Ez költséghatékonnyá teszi a gyártást.
– Hogyan készülnek ezek az elemek?
– Többféle kompozit technológiát felhasználunk a gyártáshoz. Leegyszerűsítve az eljárást a gyártás három fő lépésből áll. Első lépésben az erősítő anyagokat kiszabjuk, majd szerszámba illesztjük. Jelenleg a szerszámok nagy része egyoldalas, tehát egy formaadó oldalból és az azt lezáró vákuumfóliából áll. A szerszámba illesztjük az erősítő anyagokat, a szerszámot zárjuk, majd vákuum segítségével az előre bekevert polimer keveréket befecskendezzük. A polimer keverék a szerszámban az erősítő anyag átimpregnálását követően kitérhálósodik, megszilárdul. A teljes szilárdulást követően a terméket eltávolítjuk a szerszámból és az utómegmunkálás során kialakítjuk a végleges geometriát. A gyártási sebesség növeléséhez az alkalmazott gyanta anyagok kémiai összetételét lehet változtatni, ilyenkor reaktívabb lesz a felhasznált polimer, hamarabb térhálósódik, így a gyártási idő csökken. Nem is a megszilárdulása ideje a legfontosabb ciklusidő-csökkentő paraméter a kompozit gyártás során, a legtöbb időt az erősítő struktúra megfelelő előkészítésen lehet nyerni. A gyártási ciklusidőt a lehető leginkább a kétdimenziós textil előgyártmány automatizált kivágásával, összeállításával és előformázásával lehet csökkenteni. Fontos kérdés az, hogy hogyan tudjuk az erősítő szerkezetet a szerszámba minél gyorsabban és pontosabban behelyezni. A folyékony gyanta befecskendezése és annak térhálósodása ezzel összevetve már jóval kevesebb időt igényel, de természetesen ez is geometria függő.
– Mi viszi el a legtöbb időt?
– Mindig az alapanyagok előkészítése. A teherviselő kompozit elemekben nagyon fontos az erősítő szerkezet szálorientációja, hiszen a kompozitok alapvetően anizotróp anyagok. Ahhoz, hogy jó és tömegét, árát tekintve gazdaságos kompozit terméket gyárthassunk, az erősítő rendszert meg kell terveznünk és annak megfelelően fel kell építenünk a formaadó szerszámban. A mi kompozit termékeink javarészt üvegszállal erősített polimerek, amelybe az üvegszál különböző textíliák formájában kerül, általában több rétegben. Ezt az „építkezést” kell megkönnyítenünk azzal, hogy az anyagokat pontosan méretre vágjuk és előkészítjük. A polimerek reaktivitása, a térhálósodás sebessége is fontos paraméter, ez például a hőmérséklet növelésével is elérhető, de mint említettem az összetétel is számít.
– Mivel gyorsítható érdemben a folyamat?
– A korábban említett előkészítést, a textil előgyártmányok kialakítását nevezzük a szakmában preformingnak. A preforming lényege, hogy a kompozit teljes erősítő rendszerét minél nagyobb mértékben előkészítsük és előformázzuk, hogy az a szerszámba egyszerűen és a legrövidebb idő alatt befektethető legyen. Ez nem csak a gyorsabb gyártást, de a megfelelő minőséget is biztosítja. Ezen felül az ismétlődő, sztenderdizált alkatrészek nagyobb szériás gyártása természetesen gyorsabb, mint minden technológia esetében, különösen, ha a geometriája megengedi, egyszerűen záródó, kétoldalas szerszám alkalmazását amely szükség szerint fűthető is. A buszunk esetében vannak olyan nagy alkatrészek is, mint a középső modulok, amelyek egy része az ajtós, másik része pedig az ablakos szakasz kiképzésére szolgál. Ezek a modulok olyan szinten sztenderdizált megoldások, hogy csupán a szerszám betétek váltásával képesek vagyunk a különböző darabokat egy szerszámban legyártani. Tehát egyetlen nagy szerszámmal az összes középső modul gyártható, ami a termelést gyorsabbá és költséghatékonyabbá teszi. Habár a tervezés már ezen elvek figyelembe vételével történt, jelenleg ezt a gyártásban még nem alkalmazzuk, mert a költséghatékony megvalósításához el kell érni egy évi 250-300-as darabszámot. Körülbelül ekkortól megéri befektetni a megközelítőleg félmillió eurós szerszámozásba, amelyet egy nagyságrendileg másfél-kétmillió euró értékű gép képes bezárni. Számos kompozittechnológiai eljárás ismert, amely megfelelő megoldást kínál a darabok előállítására különböző darabszámok esetén. Célunk, hogy minden darabot zárt szerszámban, az úgynevezett RTM (resin transfer molding) eljárással gyárthassunk.
– Mivel jár még ez a módszer?
– További előny, hogy a zárt szerszámos eljárással sokkal nagyobb méretpontosságot lehet elérni az egyoldalas szerszámhoz képest. Ezzel javul a termék mechanikai tulajdonsága, az összeszerelési pontosság és a minőség is. Az utólagos megmunkálási igény is csökken, így a festésen és a felület megmunkáláson sokat tudunk spórolni.
– Milyen nagyságrendű a megrendelés volumene most a cégnél?
– A jelenlegi kapacitással háromnaponta készülhet el egy busz, így most 100 autóbuszt gyárthatunk évente. Ha ezt a megfelelő rendelésállományra alapozva meg tudnánk duplázni vagy inkább háromszorozni, azaz ha minden munkanapon kibocsáthatnánk egy buszt, akkor már megtérülhet az a nagymértékű beruházás, amely a gyorsabb és még pontosabb termelést lehetővé teszi. Az eddigi termelésünkre alapozott gazdasági számítások már igazolták ezt. Azzal, hogy elérjük a hagyományos fémvázas buszok szerkezetének az árát, a kompozit buszok verhetetlenek lesznek a piacon, figyelembe véve a kompozit alkalmazásának számtalan előnyét, mint az alacsony tömeg, alacsony fenntartási költség és korrózióállóság.
Somos József