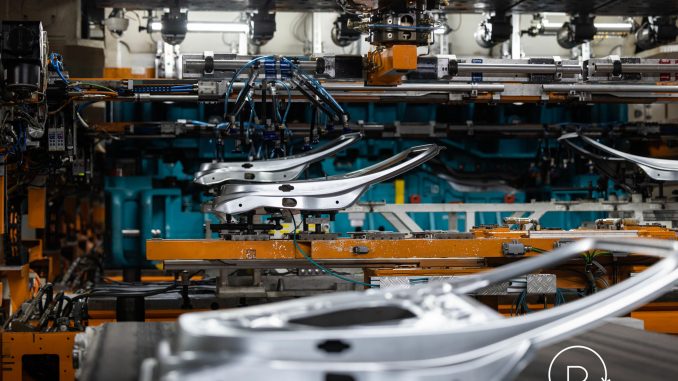
Több mint egy évszázada a futószalag határozza meg a tempót az autógyártásban. Ez a technológia azonban egyre inkább eléri a határait. A variációk szűnni nem akaró száma és az egyénre szabott lehetőségek egyre változatosabbá teszik a járműveket. Az összeszerelő rendszerek folyamatai és alkotóelemei ennek megfelelően is igen változatosak. Egy merev, a rugalmasságot hírből sem ismerő rendszerben ezt a komplexitást egyre nehezebb elsajátítani. Ezért vezeti be az Audi a világ első moduláris összeszerelő rendszerét az autóiparban, mint új és kiegészítő munka- és gyártásszervezési formát. A munkások a gyártási szigeteken a ciklusidőtől függetlenül szerelik össze az alkatrészeket. Az alkatrészek nagyfokú változékonysága miatt automatizált irányítású járművek (AGV-k) látják el ezeket az állomásokat a szükséges anyagokkal, az árutól emberig elvnek megfelelően. Jó hír, hogy ebben a technológiai kísérletben partner a 2029-től már elektromos autókat is gyártó Audi Hungaria.
A termékek növekvő összetettsége és az egyedi változatok iránti megnövekedett kereslet megváltoztatta a termeléssel szemben támasztott követelményeket. Egyre nagyobb rugalmassággal kell alkalmazkodnia az autógyártóknak az egyedi vevői igényekhez, a rövid távú piaci változásokhoz és a fenntarthatósági kérdésekhez. Egyre nehezebb egy hagyományos szállítószalag-összeállítást leképezni erre a komplexitásra. Erre a kihívásra megoldás a moduláris összeszerelés. Nincs szalag, nincs egységes munkatempó, csak rugalmas, hatékony és okos gyártás. Ingolstadtban jártunk, technikai sajtónapon tekintettük meg az okos gyártás legújabb vívmányait, koncepcióit, és a jövő gyártási technológiáit.
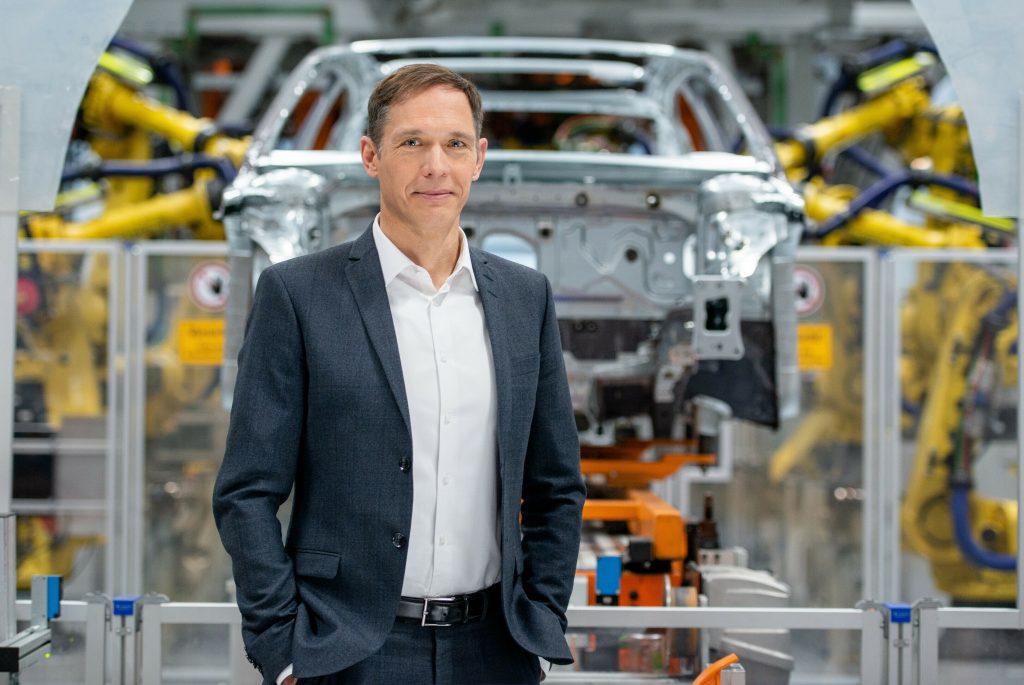
Mi a moduláris gyártás?
A koncepciót már 2016 novemberében egy hasonló ingolstadti gyárlátogatás alkalmával már megtekinthettük, a rendszer mára érett meg ahhoz, hogy kiemelt pilot projektként foglalkozzon vele az Audi, hogy a tervek szerint 2026-tól már a gyártásban is alkalmazhassák.
A merev futószalag helyett dinamikus eljárások váltják egymást, változó állomási sorrenddel és változattól függő feldolgozási időkkel, ezt a rendszert nevezhetjük immár virtuális futószalagnak. – A moduláris összeszerelés az egyik megoldásunk a termeléssel szemben támasztott jövőbeli kihívásokra – mondta el Gerd Walker, az Audi termelési és logisztikai igazgatótanácsának tagja. – A digitális technológiát céltudatosan alkalmazzuk dolgozóink érdekében, miközben rugalmasabb és hatékonyabb összeszerelést érünk el – teszi hozzá Walker, akivel az ingolstadti gyártúrán személyesen is találkozhattunk. Megerősítette, hogy lesz elektromosautó-gyártás Győrben, de ehhez 2029-ig kell várnunk, (Ingolstadtban ez már 2026-ban bekövetkezik, Neckarsulmban és a mexikói gyárban 2027-ben). Hogy ez melyik modell lesz, nem árulta el, de azt elmondta, hogy Győr javában készül a Q3 következő generációjának és az ugyanazon az alapon gyártott Cupra szabadidő-autónak a szerelésére, amit majd további villanyos modell, vagy modellek követnek.
Visszatérve a moduláris gyártásra: a rugalmas rendszer egyik nagy előnye, hogy az Audi olyan embereket is foglalkoztathat, akik fizikai korlátok miatt már nem tudnak a gyártósoron, futószalag mellett dolgozni. A bemutatón ajtóburkolatok előszerelését végezték a moduláris szigeteken, ahol feltűnt, hogy mind idősebb, tapasztaltabb kollégák dolgoztak – talán így készül az Audi a munkaerőpiac kihívásaira…
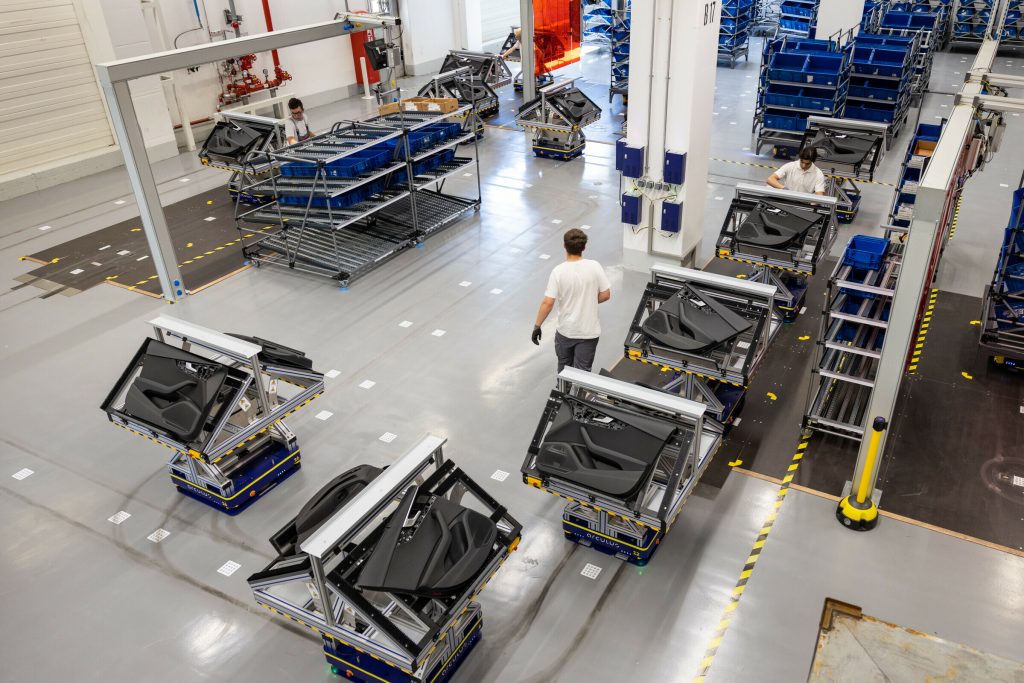
Az Audi moduláris gyártása rugalmasabb automatizálást alkalmaz, amellyel tehermentesítik az embereket. Az egységes ciklus helyett a variációtól függő feldolgozási időnek köszönhetően minden alkalmazotton kisebb a munkaterhelés. Ez lehetővé teszi az egyéni igényekhez való ergonomikus alkalmazkodást. Például egy egyszerű, csakis elektromos ablakemelővel rendelkező hátsó ajtóbelső gyártási ideje (taktidő) 42 másodperc, viszont egy hangulatfénnyel, árnyékoló rolóval szerelt bonyolultabb szerkezetre 200 másodpercnyi idő rendelkezésre. Egy hagyományos soron a hasonló darabok váltakozó érkezése többlet terhelést okoz a dolgozóknak, a moduláris szerkezetben pedig nem, minden munkafázis addig tart, amíg kell, miközben nem lassítja a sort és nem készteti kapkodásra, plusz erőfeszítésre a dolgozót.
Ki diktálja az ütemet?
A feladatok már nem követnek egységes sorrendet. Ehelyett az egyedi igényeknek megfelelően strukturáltak. Az automatizált vezetésű járművek (AGV-k, gyártója az Arculus) egyenesen arra az állomásra viszik az ajtókat (a tesztüzemben nyolc állomáson zajlott munka, az első és az utolsó egyazon sziget volt), ahol az alkatrészeket össze kell szerelni. A világító elemeket (hangulatfény, figyelmeztető LED-ek) például egy állomáson szerelik fel a kábelekkel. Ennek megfelelően a világításcsomaggal nem rendelkező munkadarabok megkerülik ezt az állomást. Egy másik állomáson egy munkás szereli be az árnyékolót, amely opcionálisan a hátsó ajtókhoz rendelhető. Az előre meghatározott tempó miatt a futószalagnál ezt a feladatot két vagy három munkás között kellene felosztani, ami nem hatékony és veszélyeztetheti a minőséget. Ha egy állomáson felhalmozódnak a munkák, az AGV-k a lehető legkevesebb várakozási idővel a következő szükséges állomásra viszik a terméket. Ezenkívül a munkaterületek konfigurációját ciklikusan ellenőrzik és kiigazítják. A futószalaggal ellentétben az egyes állomások és a moduláris gyártási rendszer nem a stabil keresletre (optimális üzemi pont) vannak kialakítva. Ehelyett egy adott spektrumon belül (optimális működési tartomány) hatékonyan működtethetők.
Nő a termelékenység
Ahol az alkatrészek variabilitása nagy, ott az áru a személyhez elv a megoldás. Például az AGV-k az ajtópanelekhez szükséges megfelelő típusú kábelkötegeket elviszik a dolgozókhoz, akik aztán a szükséges alkatrészeket veszik el. A többi azonos alkatrész visszakerül a készenléti pozícióba, mert a következő ajtópanelhez általában más alkatrészváltozatra lesz szükség. Az AGV-ken keresztül történő szortírozott alkatrészellátás feleslegessé teszi az előzetes szétválogatást. A járműveket egy rádióhálózat segítségével centiméterre pontosan lokalizálják. Az AGV-ket egy központi számítógép irányítja. Ezenkívül a minőségbiztosítási folyamatba kamerás ellenőrzés is integrálható. A szabálytalanságok így gyorsabban és egyszerűbben kezelhetők, mint egy futószalagon. Ez segít elkerülni az előre nem látható többletmunkát.
Az Audi szakemberei szerint azáltal, hogy az értékteremtésre és az önirányításra való orientációval csökkentik a gyártási időt, körülbelül 20 százalékkal növelni tudják a termelékenységet. A rugalmas hardvereknek és az automatizált irányított járműveknek köszönhetően gyakran előfordul, hogy csak a szoftvert kell módosítani. Az állomások könnyebben igazíthatók a termékekhez és az igényekhez, mint egy összekapcsolt szállítószalagon.
A jövő autógyártása
Az Audi teljesen hálózatba kapcsolt, rendkívül hatékony és fenntartható gyártást épít ki. A cél egy rugalmas, agilis és rugalmas értéklánc kialakítása, amely sikeresen megfelel a jövő kihívásainak. Ezek közé tartozik a változatok növekvő változatossága, az elektromobilitásra való átállás, az egyre változékonyabb beszállítói helyzet és a politikai bizonytalanságok. Az Audi Production Lab a moduláris összeszerelést készíti elő a sorozatgyártásra, de sok más alkalmazásban segíti a gyártástervezést.
Virtuális technológiák
Egy jövőbeli autómodell különböző kialakításai és felszereltségi változatai virtuális ábrázolások segítségével gyorsan és hatékonyan vizsgálhatók különböző környezetekben és fényviszonyok között. Az egyik sürgető cél az, hogy a lehető legkevesebb vágással kerüljön át a tervezés a gyártásba és kerüljön az ügyfelekhez az utakra. Ennek érdekében a szakértők a modell korai fejlesztési fázisától kezdve egészen az eszközök megjelenéséig megvizsgálják a tervezési tervezeteket, hogy megnézzék, reprodukálhatók-e a sorozatgyártásban. Az autók felületének végső jóváhagyása az úgynevezett adatellenőrzési mérföldkövek során történik.
Ennek legfontosabb eszközei a nagy képernyők, az úgynevezett powerwallok, amelyek lehetővé teszik, hogy az autót eredeti méretben ábrázolják – döbbenetes látvány. Kérdeztük, hogy ez egy képernyő, de aztán kiderült, hogy 4K mozigéppel vetítették az üvegre. A vizualizációs klaszterrel – egy összesen 26 ezer CPU-val rendelkező számítógépes klaszterrel – kombinálva az autókat valósághűen és fizikailag megalapozott fény-, árnyék- és visszaverődési számításokkal lehet megjeleníteni. Ez a folyamat képezi a virtuális döntéshozatali folyamat alapját. A powerwall vizualizációval együtt az Audi egyre gyakrabban alkalmaz fejre szerelhető kijelzőket. Ennek a módszernek az a nagy előnye, hogy a szakértők a virtuális modelleket az ügyfél szemszögéből is megtapasztalhatják. Mivel ez a speciális virtuális valóság rendszer szabványos hardveren és szoftveren fut, gyorsan és rugalmasan telepíthető. Sokan használhatják, és a világ más helyszínein is könnyen újrateremthető.
3D szkennelés
Ezt a technológiát a tűréskezelésben is használják. Így az Audi biztosítja, hogy egy adott modellt konstruktív és minőségi szempontból is a specifikációnak megfelelően tudjon megépíteni. A karosszéria 3D-s szimulációjával az alkatrész- és összeszerelési tűrések hatásai előre láthatóak a jármű képében. A szimuláció eredményei ezután a virtuális valóság segítségével valósághűen megjeleníthetőek. Így az Audi szakértői időtől és helytől függetlenül, szinte pluszköltségek nélkül és először a gyártóüzemekből befolyásolhatják a tervezési és fejlesztési folyamatot.
A virtuális összeszerelés-tervezés nemcsak az anyagi erőforrásokat takarítja meg, hanem innovatív, rugalmas együttműködést tesz lehetővé a különböző helyszíneken. Megszünteti a prototípusok építésének szükségességét a tervezési folyamat során. A szkennelési folyamat háromdimenziós pontfelhőket generál, amelyek segítségével virtuálisan visszatervezhetők a gépek és az infrastruktúra. A szoftver mesterséges intelligencián és gépi tanuláson alapul. Lehetővé teszi, hogy az Audi munkatársai virtuálisan navigáljanak a szerelősorokon. A Volkswagen ipari felhője hatékony eszközt ad számukra, amellyel például összehasonlíthatják a helyszíneket, és a tervezés során más gyártósorok megfelelő megoldásait használhatják.
Robotkutyát is bevetnek
Az Audi a NavVisszal együttműködve teszteli a Spot nevű robotkutyát, hogy a lehető leghatékonyabban végezhessék a 3D-s szkenneléseket. Mintegy négymillió négyzetmétert és 13 üzemet érintettek a telephelyek digitalizálásának 2017-es kezdete óta, Győrben is jártak. 100 ezer négyzetméter szkennelése – például az Audi A6 gyártásában Neckarsulmban – körülbelül három hetet vesz igénybe egyműszakos üzemben. A szkenneléseket csak éjszaka vagy hétvégén lehet elvégezni. Ráadásul az olyan szerkezeti akadályok, mint a lépcsők és ajtók, megnehezítik a szkennelési munkát. Ezzel szemben Spot, a robotkutya 48 óra alatt képes elvégezni ezt a szkennelést, és önállóan megtalálni az útvonalát. Az Audi 2021 decembere óta intenzíven teszteli Spotot. – A teszteredmények rendkívül ígéretesek, és rendszeresen frissíthetők – mondta el nekünk André Bongartz projektvezető. – Folyamatosan érkeznek a bemeneti adatok, amelyeket felhasználhatunk az új autómodellek tervezésénél. A virtuális képekbe a 3D szkennelések bármelyikét be lehet építeni, amiért Andrés Kohler csapata felel. – Az összes tervezési adat egyesítése a digitális ikertestvérünkben évekre előre holisztikus képet ad a jövőbeli gyártási terveinkről – magyarázta Kohler. Mint egy valódi gyárban, az új Audi modell mellett a műhelytér, a szállítószalag-technológia, a szerszámok, a polcok és a konténerek is szerepelnek.
Az összeszerelési sorrendeket és a logisztikai szempontokat nagyrészt interdiszciplináris csapatok tervezik és optimalizálják az úgynevezett 3D folyamatműhelyekben. A digitális ikernek és egy házon belüli VR-megoldásnak köszönhetően az Audi kihasználja a digitalizáció és a vizualizáció előnyeit. Ezek közé tartoznak a naponta frissülő alkatrészadatok és a különböző autóváltozatok megtekintése. – Mindenekelőtt a gyártást abból a szempontból nézzük, hogy később hogyan fog kinézni az egész – magyarázta Andrés Kohler. Hangsúlyozza, hogy az együttműködés továbbra is központi elem marad: – Mindig újra és újra lenyűgöz a pillanat, amikor felvesszük a VR-szemüveget, és avatárként találkozunk a kollégáinkkal a virtuális világban. Először ott építjük meg az új Audinkat, vagy megnézzük egy számítógépen generált avatárt, és azt, hogy az hogyan alkalmazható valós idejű szimulációként. És ha szükséges, miközben együtt vagyunk ott, megbeszéljük és optimalizáljuk a szekvenciákat és a munkakörnyezetet, például azt, hogy hogyan állítsuk be az anyagokat, milyen eszközökre van szükség.
Fenntartható gyártás
Az Audi ingolstadti telephelye egy év alatt annyi energiát fogyaszt, mint amennyit az egész város. Az adatok és az adatelemzés alapvető eszközök az energiatakarékossághoz. Az Audi saját fejlesztésű energiaanalitikai eszköze segít a gyártás fenntarthatóvá tételében az erőforrások kímélése mellett. Lehetővé teszi, hogy rámutassunk a magas energiafogyasztásra a gyártás során és a gyártáson kívüli időszakokban. Először is, a szakértők különböző forrásokból egységes adatformátumban gyűjtik össze az adatokat. Összegyűjtik például az elkészült járművek és alkatrészek adatait, a szórókabinok vagy hegesztőpisztolyok energiaadatait, valamint az épületek világításának és szellőztetésének fogyasztására vonatkozó információkat. A következő lépésben átláthatóvá teszik az energiafogyasztást az energiaügyi tisztviselők számára, akik ezt felhasználhatják az energiafelhasználás elemzéséhez. Ha az energiaszükséglet meghaladja a korábban meghatározott tűréshatárokat, felmérhetik az okokat, és lépéseket tehetnek a termelés alatti fogyasztás csökkentésére, vagy akár az alapterhelés csökkentésére a termelési területeken. 2021-ben az Audi az Energy Analytics és a folyamatfejlesztések segítségével mintegy 37 000 MWh-t tudott megtakarítani az ingolstadti telephelyén.
Mesterségei intelligencia a gyártásban
A mesterséges intelligencia (MI) és a gépi tanulás az Audi digitális átalakulásának és modern gyártásának alapvető technológiái. Az ingolstadti présüzemben egy MI-algoritmus segít azonosítani az alkatrészek hibáit. Ezt az eljárást egy mesterséges neurális hálózaton alapuló szoftver támogatja. A szoftver maga azonosítja a legkisebb hibákat is, és megbízhatóan megjelöli azokat. A megoldás alapja a mélytanulás, a gépi tanulás egy speciális fajtája, amely strukturálatlan és nagy dimenziós adatmennyiségekkel is képes dolgozni. A csapat több millió tesztmintát használt fel a mesterséges neurális hálózat hónapokon át tartó betanításához. Ez az adatbázis több terabájtnyi ilyen képet tartalmaz, amelyek az Audi és a Volkswagen több telephelyének nyomdáiból származnak.
Egy másik kísérleti projektben az Audi mesterséges intelligenciát használ a ponthegesztések minőségének ellenőrzésére a nagyszériás gyártás során a neckarsulmi telephelyén. Egy Audi A6-os karosszériájának alkatrészeit körülbelül 5300 hegesztési ponton kell összekötni egymással. Eddig a gyártó személyzet véletlenszerű ultrahangos elemzésekkel ellenőrizte az ellenállásponthegesztés minőségét. A WPS Analytics kísérleti projekt részeként a szakértők mesterséges intelligencia segítségével automatikusan, valós időben észlelik a minőségi rendellenességeket. Jelenleg az algoritmust, a műszerfalat és a mély minőségelemző alkalmazást az A6 és A7 karosszériájának megépítéséhez használják. Ez a hálózatba kapcsolt gyártás más alkalmazásainak tervrajza.
Egy másik innováció győri, az ingolstadti technikai nyílt napon Schönberger Rajmund és kollégája bemutattak egy olyan házon belül fejlesztett kamerás ellenőrző rendszert, amelyet a lakkozóban használnak a nem megfelelő vagy hiányos tömítések kiszűréséhez. Amióta ezt használják (2021 közepétől folyamatosan üzemel), megszűntek a járműszereldei reklamációk. Nagy esély van arra, hogy a magyarok innovációját konszernszinten is alkalmazzák majd.
B. Cs.